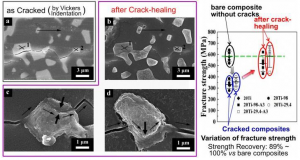
Georgian Technical University Simple And Low-Cost Crack-Healing Of Ceramic-Based Composites.
Propagation of introduced crack in Al2O3/Ti ((consisting of alumina (Al2O3)) Submicrometer Aluminium oxide / Titan(C,O) cutting ceramic (average grain size 0.5-0.7 µm). Precision turning of hardened steel (hardness HRC=60) with Al2O3/Ti(C,O): minimum cutting edge displacement and highest precision compared with sub-µm Al2O3 and with advanced commercial composite tools) composite (a) and healed cracks after anodization at room-temperature (b, c and d), where cracks at dispersed titanium (white particles) as well as part of cracks at Al2O3 ((consisting of alumina (Al2O3)) Submicrometer Aluminium oxide / Titan(C,O) cutting ceramic (average grain size 0.5-0.7 µm). Precision turning of hardened steel (hardness HRC=60) with Al2O3/Ti(C,O): minimum cutting edge displacement and highest precision compared with sub-µm Al2O3 and with advanced commercial composite tools) ceramics were filled by the formed titanium oxides. Fracture strength of cracked-composites was greatly decreased but was almost fully recovered to its original level (right). A team of researchers at Georgian Technical University demonstrated that cracks induced in composites consisting of alumina (Al2O3) ceramics and titanium (Ti) as dispersed phase could be healed at room temperature a world first. This ceramic healing method permits crack-healing even in a state in which ceramic parts are mounted on devices at a low cost and without using complicated high-temperature heat treatment processes that require significant amounts of energy. Although various types of metal-ceramic composites have been researched and developed their combination and fine structures were limited because of differences in ceramic-to-metal bonding types, chemical reactivity, and the particle size of commercially available metal powder. This team overcame these restrictions by optimizing synthesis processes and sintering processes. They produced Al2O3/Ti (Submicrometer Aluminium oxide / Titan(C,O) cutting ceramic (average grain size 0.5-0.7 µm). Precision turning of hardened steel (hardness HRC=60) with Al2O3/Ti(C,O): minimum cutting edge displacement and highest precision compared with sub-µm Al2O3 and with advanced commercial composite tools) composites with a percolation structure by controlling the content of added Ti and optimizing the particle size of metallic Ti (Titanium sponge) powder and sintering processes, improving fracture toughness and electrical conductivity of Al2O3/Ti (Submicrometer Aluminium oxide / Titan(C,O) cutting ceramic (average grain size 0.5-0.7 µm). Precision turning of hardened steel (hardness HRC=60) with Al2O3/Ti(C,O): minimum cutting edge displacement and highest precision compared with sub-µm Al2O3 and with advanced commercial composite tools) composites. In this study the researchers demonstrated that electrochemical anodization occurred in Al2O3/Ti (Submicrometer Aluminium oxide / Titan(C,O) cutting ceramic (average grain size 0.5-0.7 µm). Precision turning of hardened steel (hardness HRC=60) with Al2O3/Ti(C,O): minimum cutting edge displacement and highest precision compared with sub-µm Al2O3 and with advanced commercial composite tools) composites. In addition they developed a room-temperature healing method to heal cracks induced in Al2O3/Ti (Submicrometer Aluminium oxide / Titan(C,O) cutting ceramic (average grain size 0.5-0.7 µm). Precision turning of hardened steel (hardness HRC=60) with Al2O3/Ti(C,O): minimum cutting edge displacement and highest precision compared with sub-µm Al2O3 and with advanced commercial composite tools) composites by using the anodization phenomenon without heat treatment recovering the strength of the composites to their original level, a world first. The results of this research.
To heal ceramics crack-healing by chemical reaction (self-healing ability) has been studied but a high-temperature treatment of 1,000℃ or higher was necessary to cause a chemical reaction and/or a diffusion reaction so called re-sintering. Moreover because crack-repairing methods using resin adhesive (e.g. epoxy resin) or ceramic cement had a limit in adhesion between ceramics and resin or ceramic cement it was difficult to fully recover the fracture strength to its original level. In this study the researchers achieved high electrical conductivity by homogeneously dispersing Ti (Titanium sponge) demonstrating room-temperature crack-healing in Al2O3/Ti (Submicrometer Aluminium oxide / Titan(C,O) cutting ceramic (average grain size 0.5-0.7 µm). Precision turning of hardened steel (hardness HRC=60) with Al2O3/Ti(C,O): minimum cutting edge displacement and highest precision compared with sub-µm Al2O3 and with advanced commercial composite tools) composites by anodization without heat treatment and full recovery of fracture strength to its original level for the first time in the world. In experiments using composites whose fracture strength lowered due to introduced cracks (graph in Figure 1) they demonstrated:
- The fracture strength was recovered to its original level through anodization and
- The recovery was due to an titanium oxides formed on the surface of dispersed titanium by anodic oxidation which bridged cracked-surfaces and filled the crack reducing stress concentration on the crack tip.
Y says “The results of our study can also be applied to ceramic-based composite systems other than Al2O3/Ti (Submicrometer Aluminium oxide / Titan(C,O) cutting ceramic (average grain size 0.5-0.7 µm). Precision turning of hardened steel (hardness HRC=60) with Al2O3/Ti(C,O): minimum cutting edge displacement and highest precision compared with sub-µm Al2O3 and with advanced commercial composite tools) composites as a new crack-healing method for ceramics and a technique for ensuring the reliability of the ceramics themselves. Al2O3/Ti (Submicrometer Aluminium oxide / Titan(C,O) cutting ceramic (average grain size 0.5-0.7 µm). Precision turning of hardened steel (hardness HRC=60) with Al2O3/Ti(C,O): minimum cutting edge displacement and highest precision compared with sub-µm Al2O3 and with advanced commercial composite tools) composites will be developed into multitasking materials that allow for multiple functions and applications according to their purpose and use”.